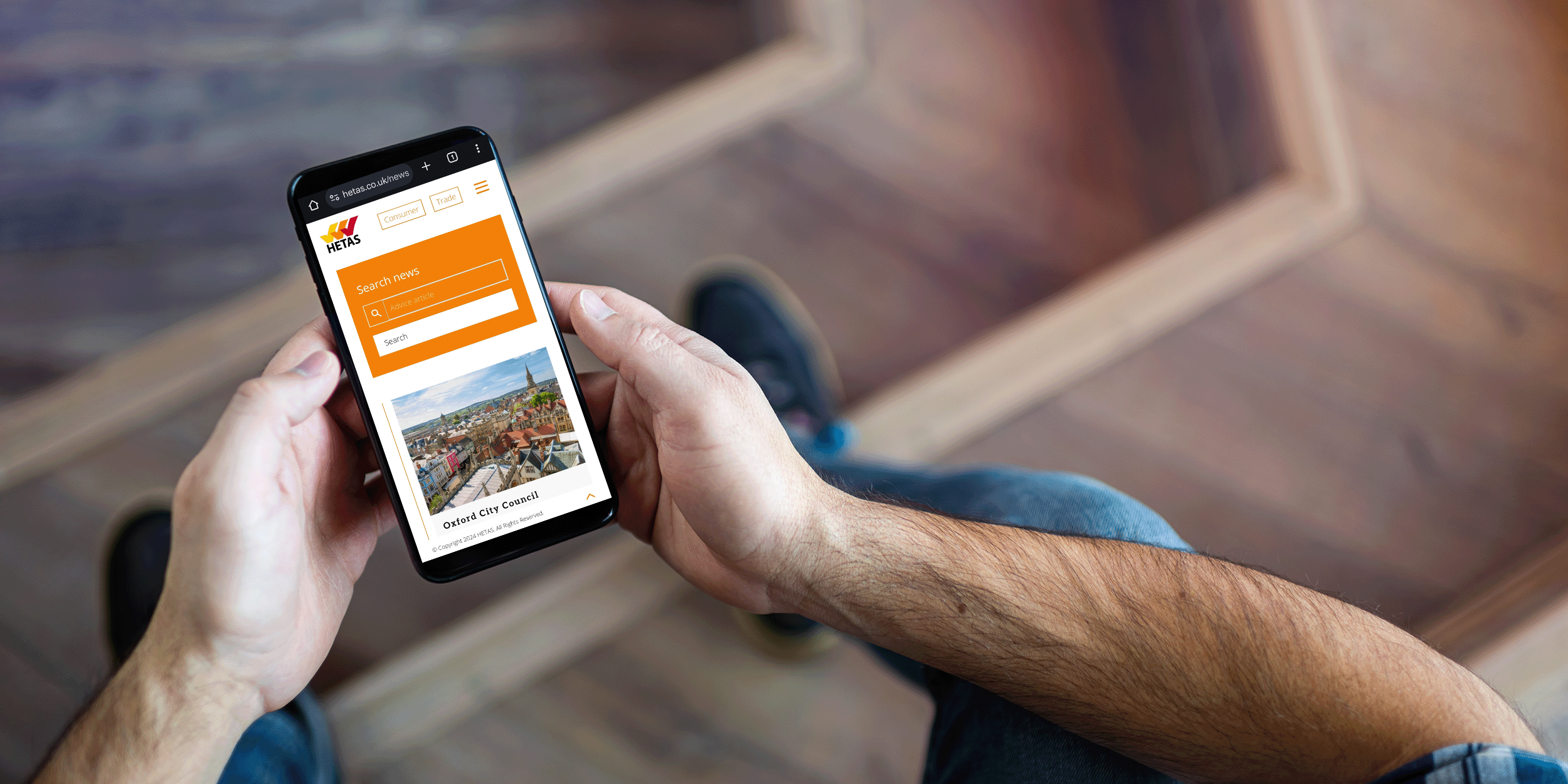
Approved Document J
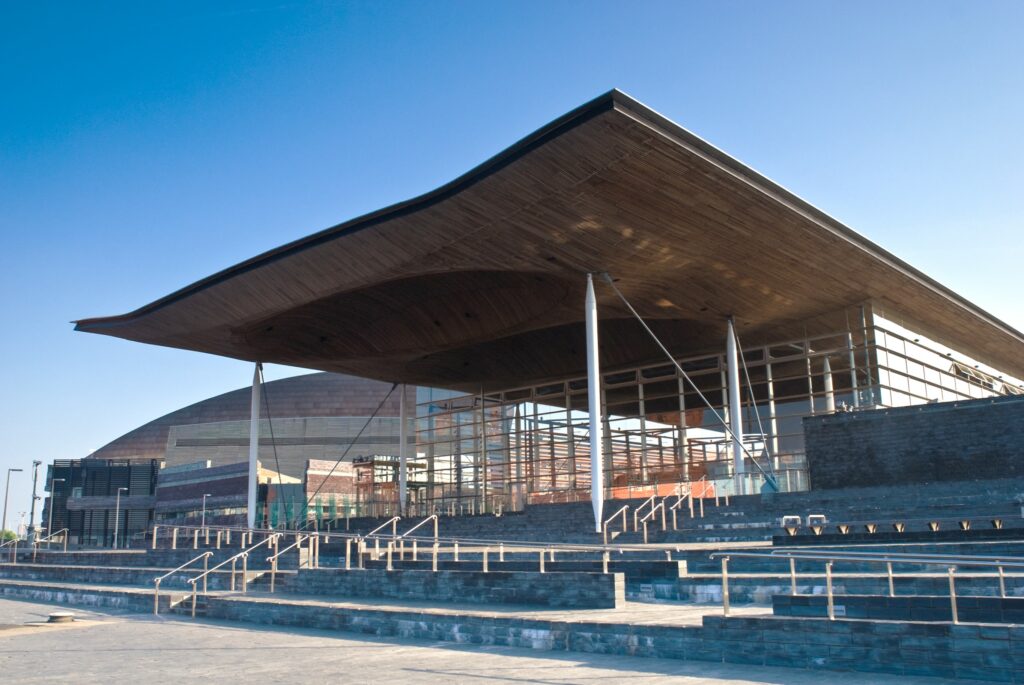
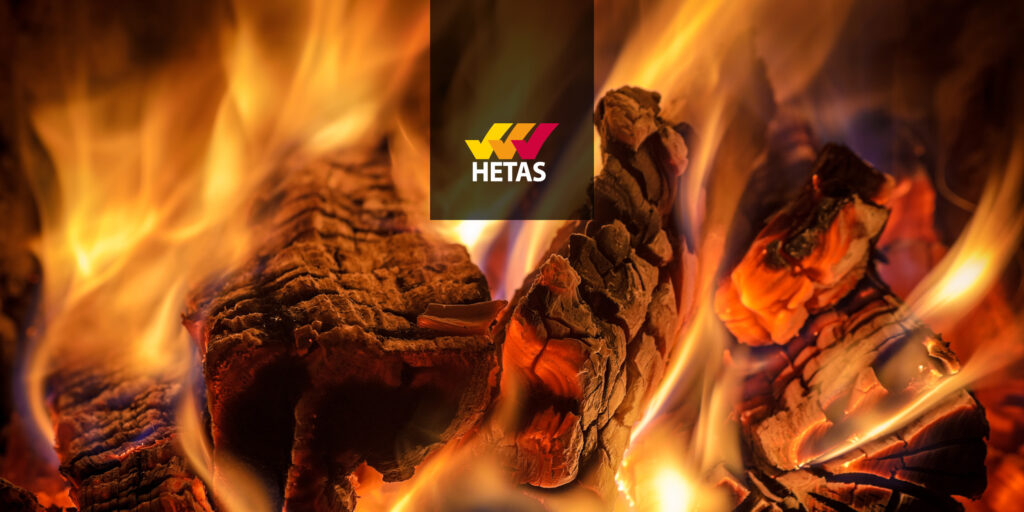
Working with Building Control
Working with Building Control (Appendix A) as part of Approved Document J A recent roundtable hosted by HETAS revealed a number of issues that are affecting both the biomass and wood-burning stoves markets. One of the key areas of discussion was the issues surrounding the ‘signing off’ or ‘notification’ of solid fuel & biomass installations and…
Posted on February 4, 2016 by Alun
Posted in