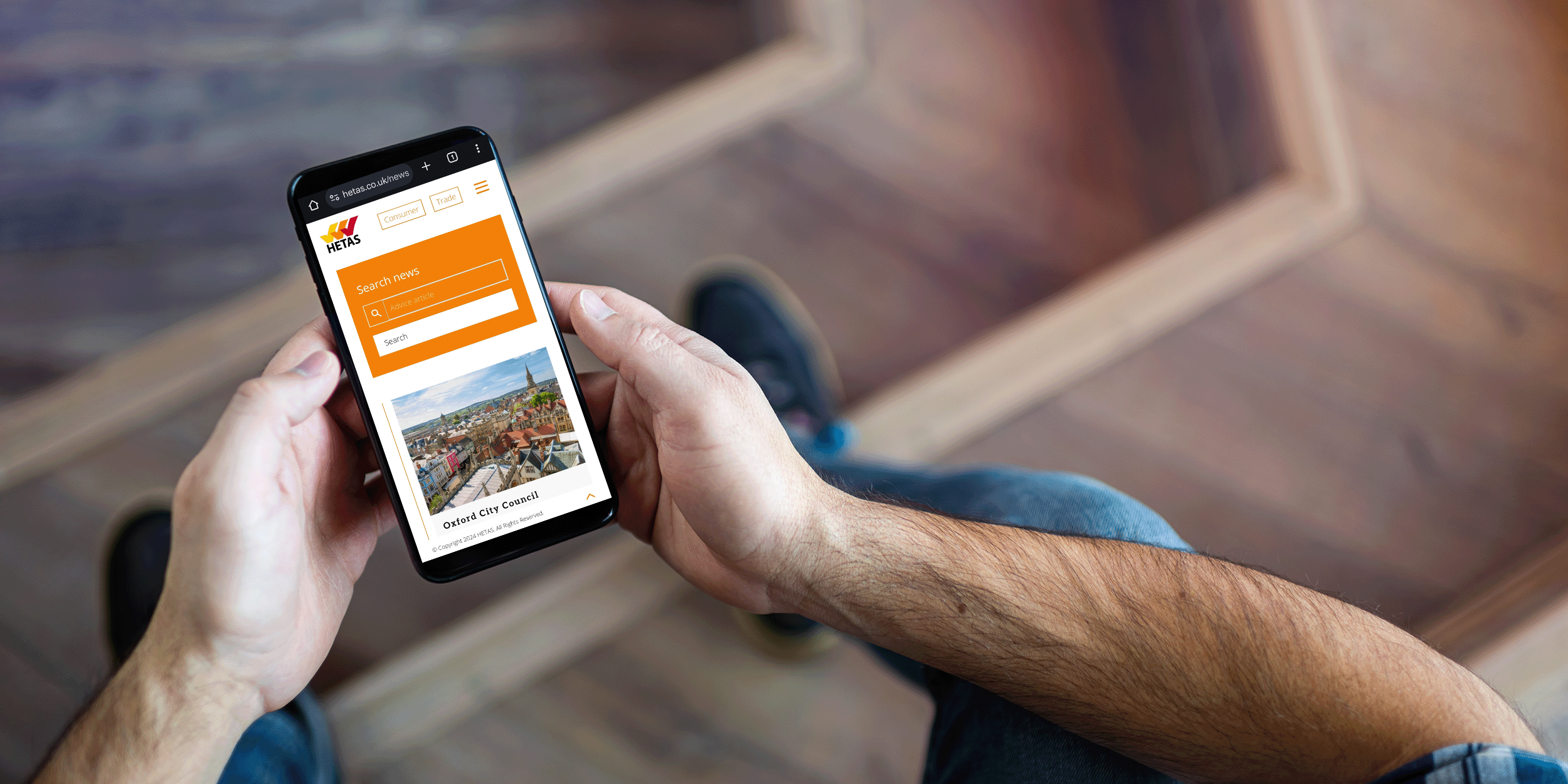
HETAS News
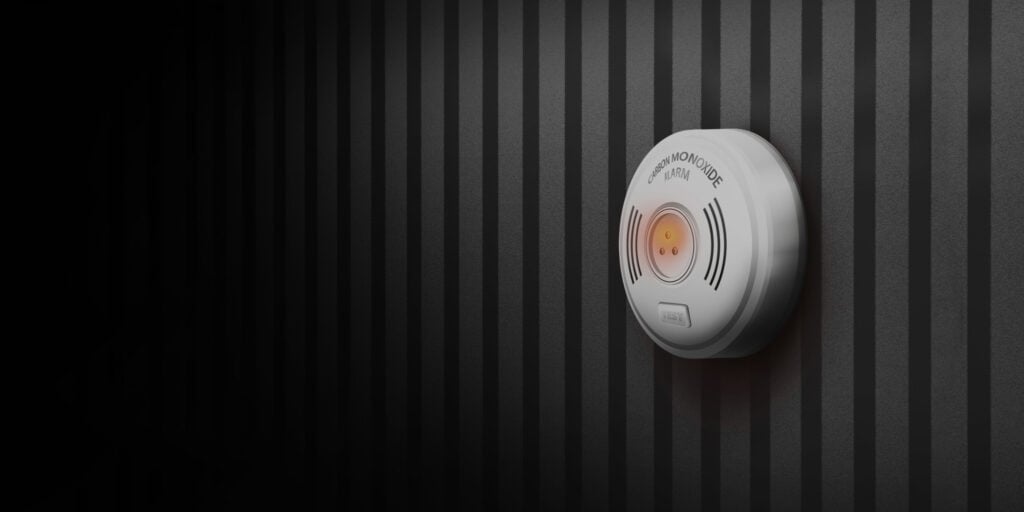
Carbon Monoxide Awareness Week
Carbon Monoxide (CO) Awareness Week 2024 takes place 18–24 November this year, and HETAS are continuing to support the campaign.
Posted on November 17, 2024 by Charlie
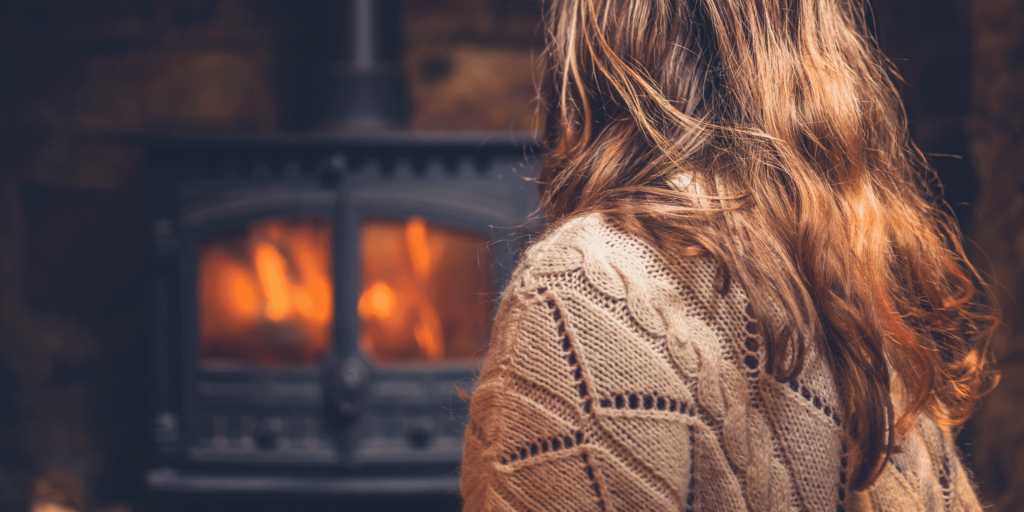
Burn Better
Defra has launched its Burn Better, Breathe Better campaign for the 2023/24 heating season.
Posted on October 27, 2023 by Alun
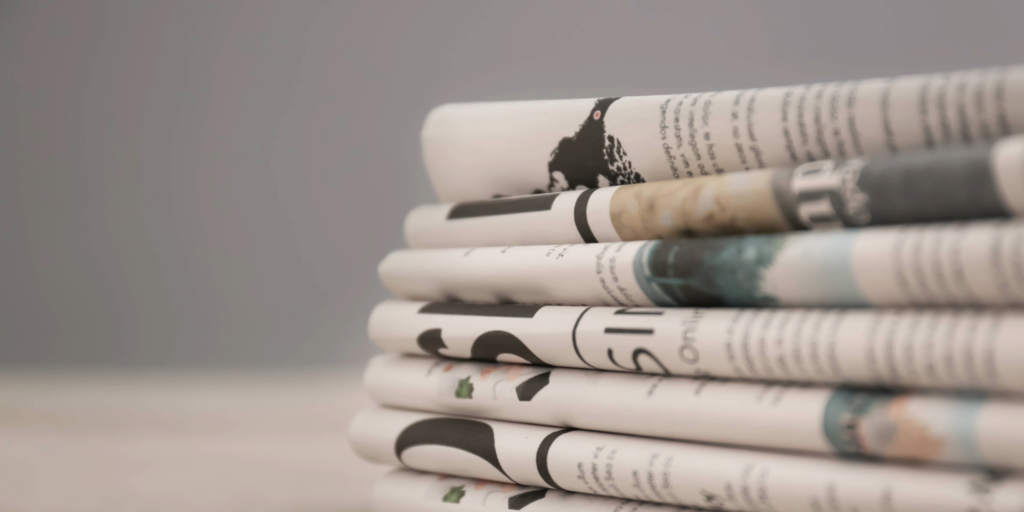
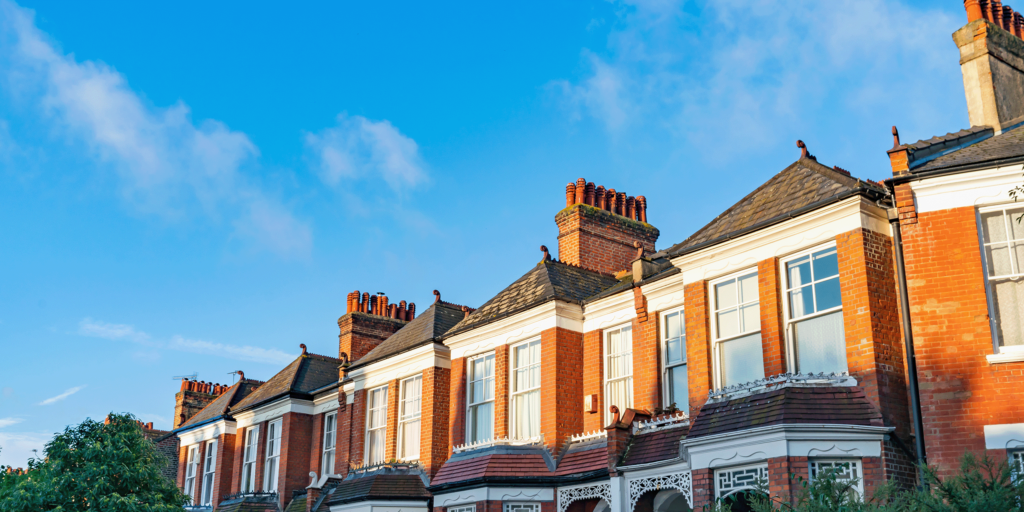
Chimney Fire Safety Week 2024
Chimney Fire Safety Week is back for 2024! The annual campaign takes place this September. What will you be doing to support the campaign this year?
Posted on August 29, 2023 by Alun
Posted in
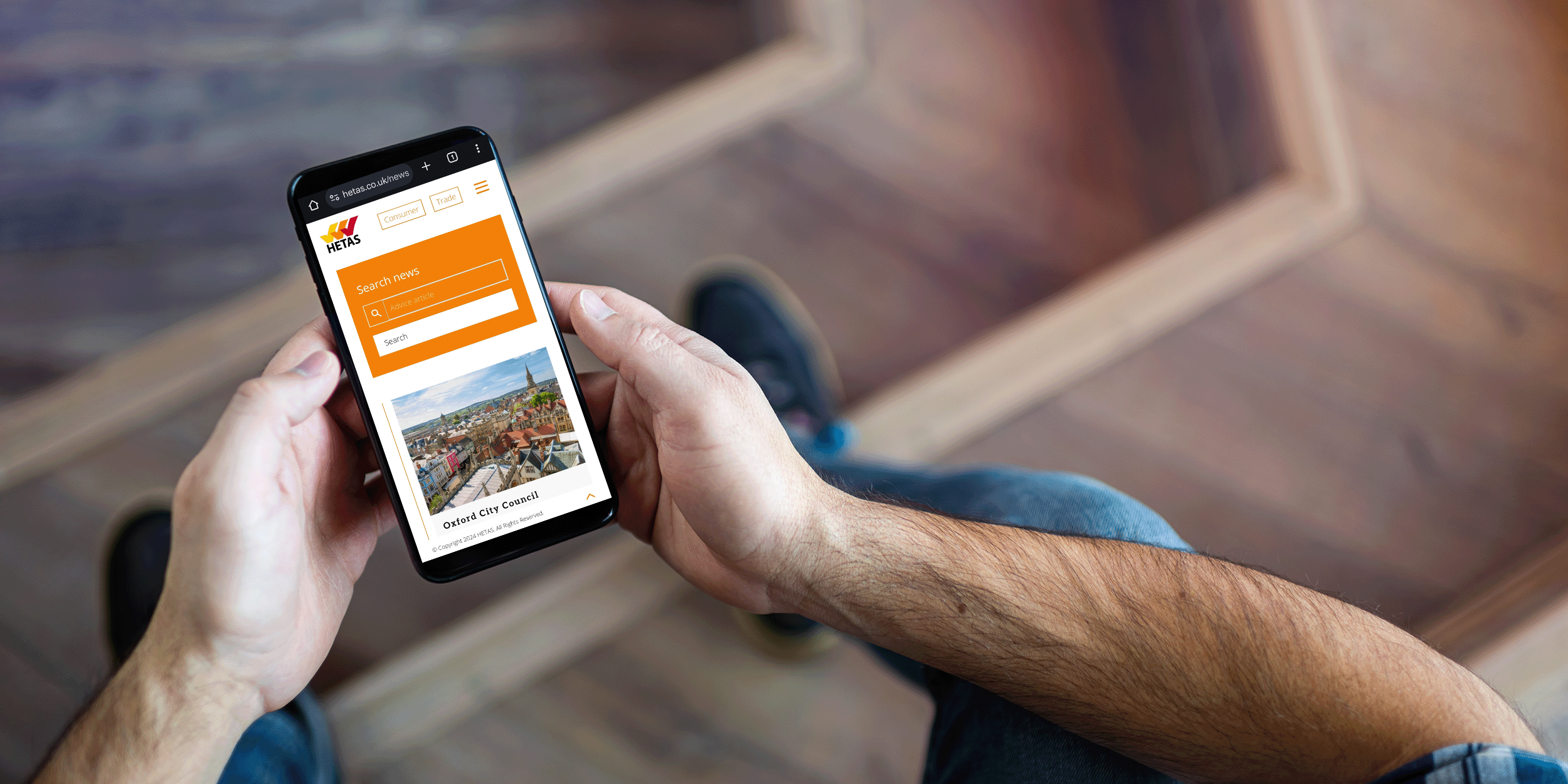
Ban on wood stoves? | Government confirms no ban
No doubt you will have seen some headlines about a possible ban on wood stoves. Here, we identify the truth behind the headlines and what measures the government is undertaking in relation to domestic burning.
Posted on March 7, 2023 by Alun
Posted in
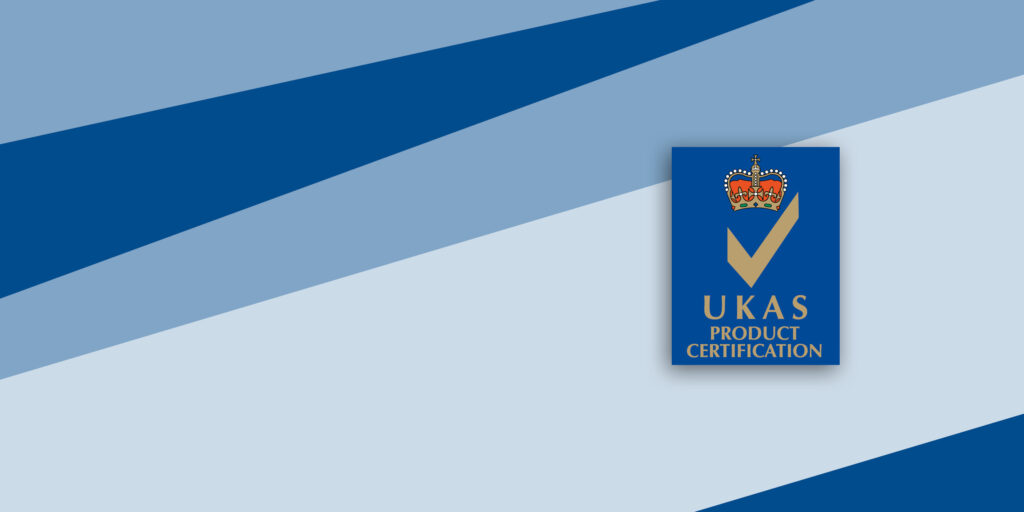
UKAS Audit success for HETAS
HETAS welcomed the UKAS audit team during early February for its annual independent audit of our regulated services.
Posted on February 27, 2023 by Alice
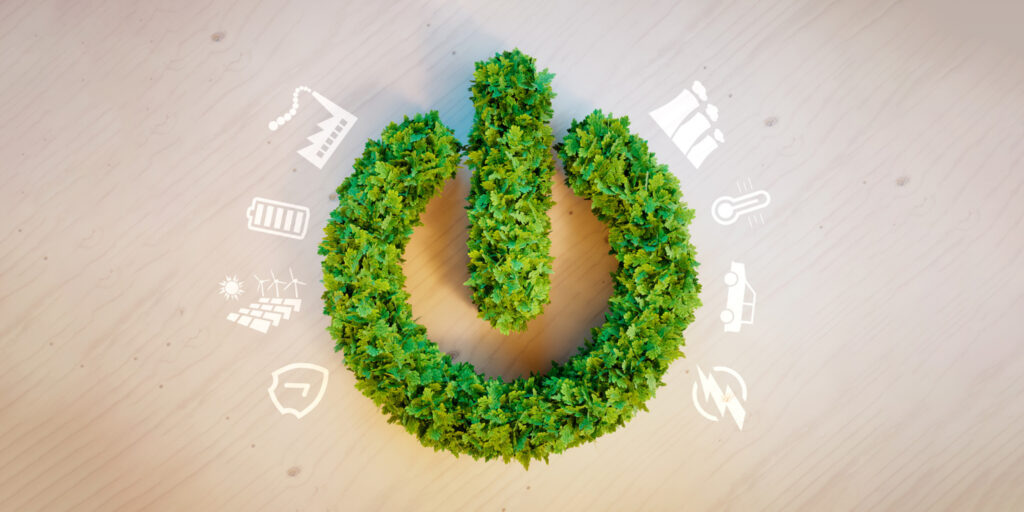
Boiler Upgrade Scheme now open
The £450 million Boiler Upgrade Scheme (previously known as the Clean Heat Grant) is part of more than £3.9 billion of new funding being announced by the government for decarbonising heat and buildings. This will fund the next 3 years of investment through the Social Housing Decarbonisation Fund, the Home Upgrade Grant scheme, the Boiler…
Posted on April 28, 2022 by Alun
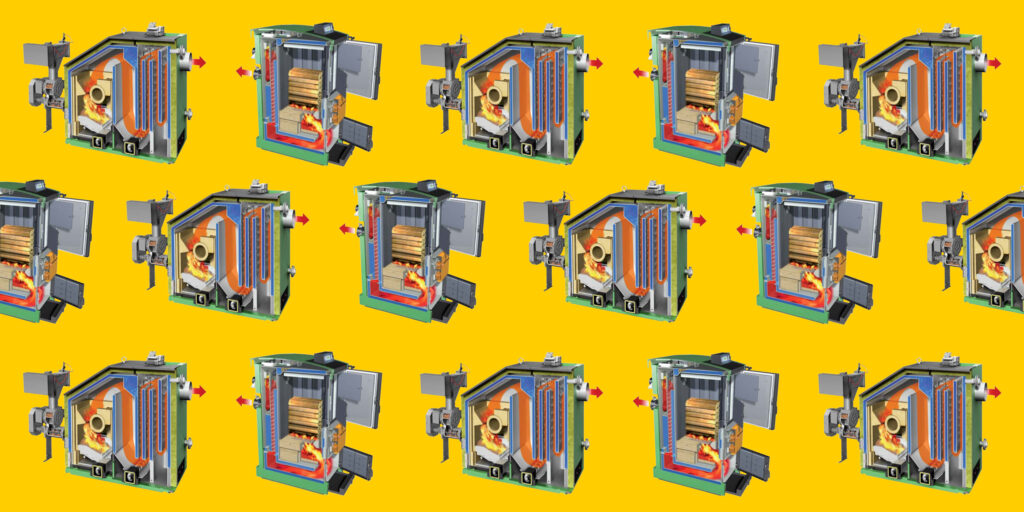
Biomass maintenance requirements
Incoming legislation this April will pay dividends for installers, non-domestic biomass heating owners and the environment, says HETAS. As of April 2022, updates to The Domestic Renewable Heat Incentive Scheme and Renewable Heat Incentive Scheme (Amendment) Regulations 2022 will make it a legal requirement to prove biomass heating systems in non-domestic settings have been properly…
Posted on March 29, 2022 by Alun
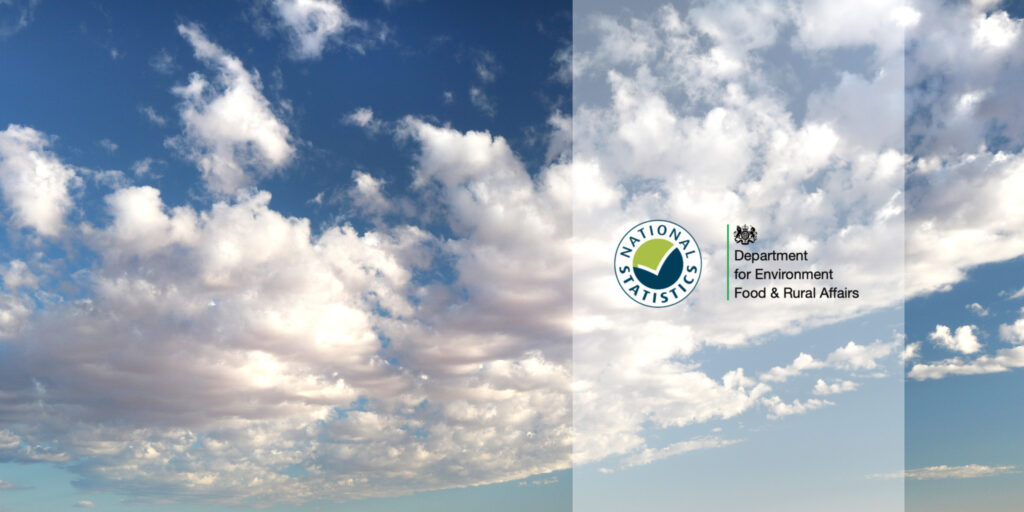
National statistics of emissions of air pollutants
On the 18th February 2022 Defra published its emissions of air pollutants national statistics. The publication provides estimates of UK emissions of particulate matter (PM10 and PM2.5), nitrogen oxides, ammonia, non-methane volatile organic compounds and sulphur dioxide. The information contains statistics on annual emissions for the period 1970 to 2020. The full set of emissions…
Posted on February 24, 2022 by Alun
Tagged
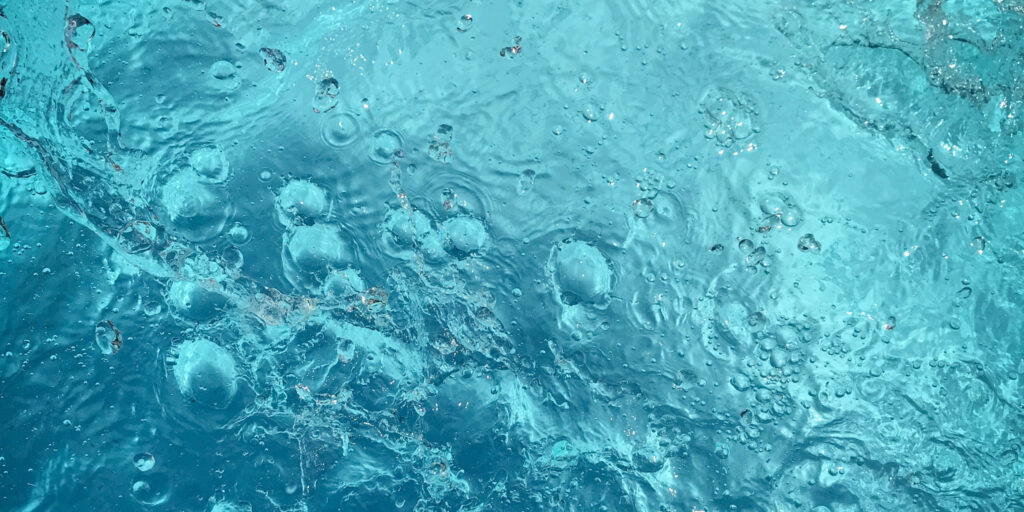
Boiler Upgrade Scheme
Through the Heat and Buildings Strategy, the government in October 2021 published plans to incentivise people to install low-carbon heating systems in a simple, fair and cheap way as they come to replace their old boilers over the coming decade. This will significantly reduce the UK’s dependency on fossil fuels and exposure to global price…
Posted on February 23, 2022 by Alice